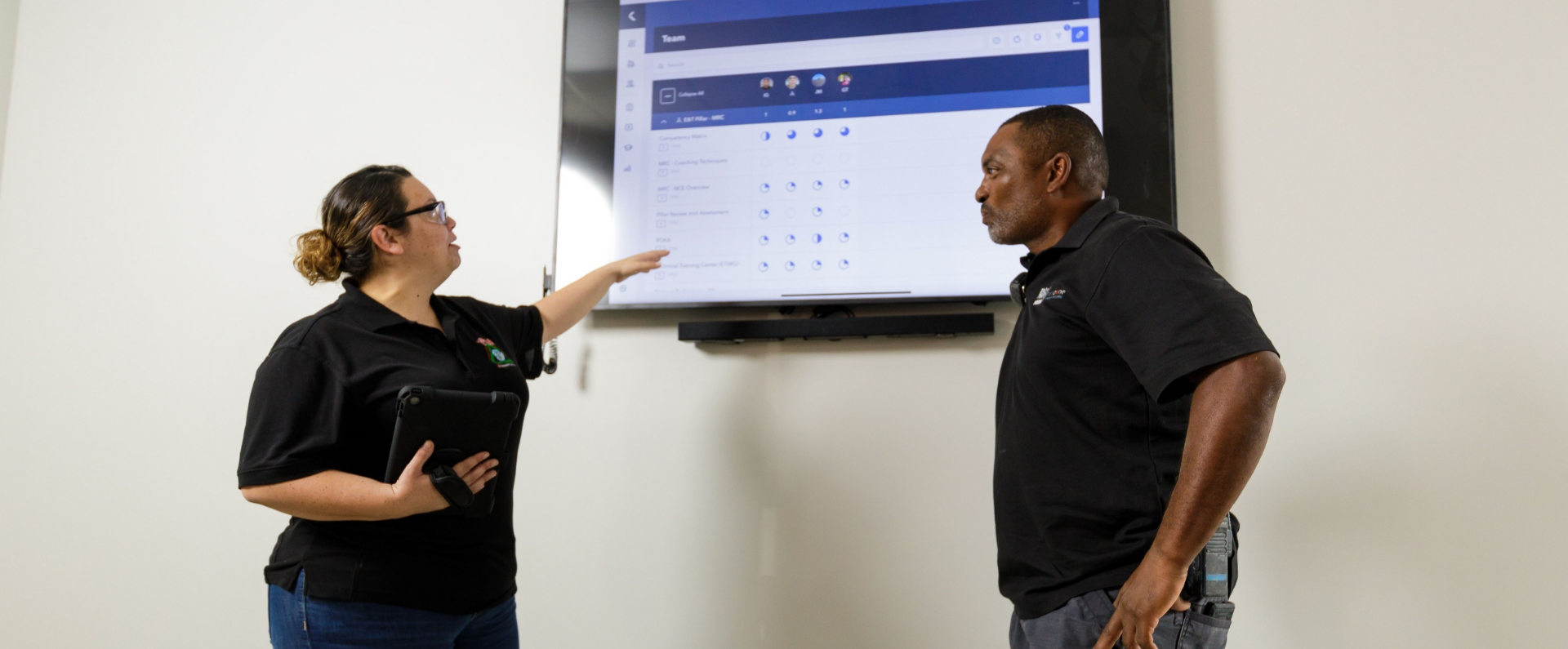
Onboarding in Our Factories: Training for Success
Historically, our manufacturing facilities have transitioned knowledge on a heavily local basis, a practice common to the industry. The same concept has been applied to our onboarding processes in the factories in the past. While this approach can effectively train associates in their area of expertise, it can also leave gaps in a more full, holistic understanding of our manufacturing operations, equipment, and ways of working in our facilities across the country. Through an emerging, revamped onboarding and development initiative, we are applying a hands-on learning structure to the manufacturing side of our business.
Michael, Training Director for Technical Operations, says, “By leveraging learning principles like the 70/20/10 rule (i.e., individuals tend to gain 70% of their knowledge from challenging experiences and assignments, 20% from developmental relationships, and 10% from coursework and training) and applying a structure that focuses on milestones throughout the first 120 days of employment, we can consistently set new people coming to our organization up for success.”
With rising business needs, facility expansions, and a continuous improvement mindset, our teams are constantly growing in volume and capabilities. With many years of experience in the manufacturing industry, Michael goes on to explain, “Due to tenured and high seniority associates entering retirement, there are fewer people available to deliver onboarding messages through local knowledge as the next generation of factory leaders are coming in the door. Today’s learners are not yesterday’s learners—we had to consider how we implement digital connection and cutting-edge technology to deliver engaging training and development experiences to new associates.”
As a result, we have begun adapting our onboarding processes in a way that prioritizes our associates’ comprehension in a safe, education-based environment with an emphasis on safety, quality, and learning. “We're standing up material learning materials and we're also creating these environments called learning centers to simulate experiences a new associate might encounter on the factory floor in a classroom-like setting,” says Michael.
This allows our associates to apply what we call our principles of operations in a hands-on, growth-focused environment before they are asked to apply it on the factory floor. Learning centers give our employees the chance to practice a skill, achieve a certain level, and safely replicate it in a fast-paced, dynamic manufacturing environment. This creates more confident and skillful individuals championing our manufacturing processes, as well as more opportunity for associates to further develop their skill sets and grow their careers at any stage with us.
Our hope is to instill an emphasis on continuous learning and continuous improvement at a foundational level when we consider how we onboard in our factories. Additionally, this updated approach is designed to accelerate the time it took in the past for someone to be trained up to the next level of their career path. By being purposeful in the base-level skills being coached on and lesson delivery for new associates, we can make a positive impact on individual careers, our teams’ efficiency, and the larger business as we enhance the lives of pets and pet owners through quality pet food and care products.
Interested in becoming one of the future leaders in our factories? Join our talent network to be alerted of the most relevant job opportunities matching your skillset.
Explore our manufacturing job openings and build your career with an industry leader.